Composites play a significant role in many sectors, including aerospace, automotive, marine, construction, and renewable energy. Composite materials like fibreglass, carbon fibre, and reinforced polymers offer numerous advantages: they are durable, lightweight, and highly resistant to damage. However, the increasing use of composite materials has also led to a surge in the amount of waste generated.
Unfortunately, there are limited effective and sustainable End-of-Life (EoL) solutions available for composite waste today. The improper handling and disposal of these materials add to the growing pressures on landfill sites and can result in persistent environmental damage. It is essential for industries reliant on composite materials to address the transition to a circular economy model to reduce environmental impact and support sustainability efforts.
This article examines:
- the escalating problem of composite waste,
- how much composite waste the fast-growing aviation, wind energy, and automotive sectors generate,
- current legislation that affects composite waste,
- current initiatives and collaborations to tackle composite waste in the aerospace, wind energy, and automotive sectors,
- the importance of traceability for effective management of composite waste across industries.
The problem and challenges with composite waste
Carbon and glass fibre composites (CFRP & GFRP), commonly used in wind turbine blades, hydrogen storage tanks, aircraft, yachts, buildings, and automobiles, are expected to become a major source of waste worldwide.
By 2050, it is estimated that the aircraft and wind turbine industries will collectively generate an annual CFRP waste total of 840,300 tonnes.1 In Europe, the total composite waste is projected to reach an astounding 683,000 tonnes per year by that time, while the global recycling capacity lags behind at less than 100,000 tonnes.2
Predominantly sourced from finite fossil fuels, composite materials present significant recycling challenges due to high manufacturing scrap rates and complex material compositions. The recycling process is further complicated as information about material composition is often lost by the time the materials reach their end-of-life stage, complicating recycling efforts.3
However, the disposal of composite materials presents unique challenges due to the durability of the resins and fibres that compose them. It can take hundreds or thousands of years for them to fully break down. The hazardous substances present in composite waste can release toxic substances into the soil and groundwater when not disposed of properly, posing a serious risk to the environment and the lives of those living nearby.
Which industries generate the most composite waste?
Composite waste is generated by a wide range of industries due to the versatile nature of composite materials. These industries typically use composites for their advantageous properties, such as high strength-to-weight ratios, corrosion resistance, and design flexibility. Here are three industries that are known to generate significant amounts of composite waste that are projected to grow substantially in the future.
Aerospace
Aerospace manufacturers extensively use advanced composites for various aircraft components due to their high strength-to-weight ratio and durability. As aircraft reach the end of their service life, the composite materials used in their construction become a source of waste.
Aircraft boneyards, which are spread out across the globe, also encounter the same issue of managing large amounts of composite waste. The Aircraft Fleet Recycling Association (AFRA) estimates around 15,000 aircraft will be retired in the next 2 decades.4 Composite waste from aircraft typically represents a significant portion of the total waste, as since 2005 there has been an increasing replacement of structural weight with lighter,5 yet more combustible composite material,6 which can take thousands of years to decompose.
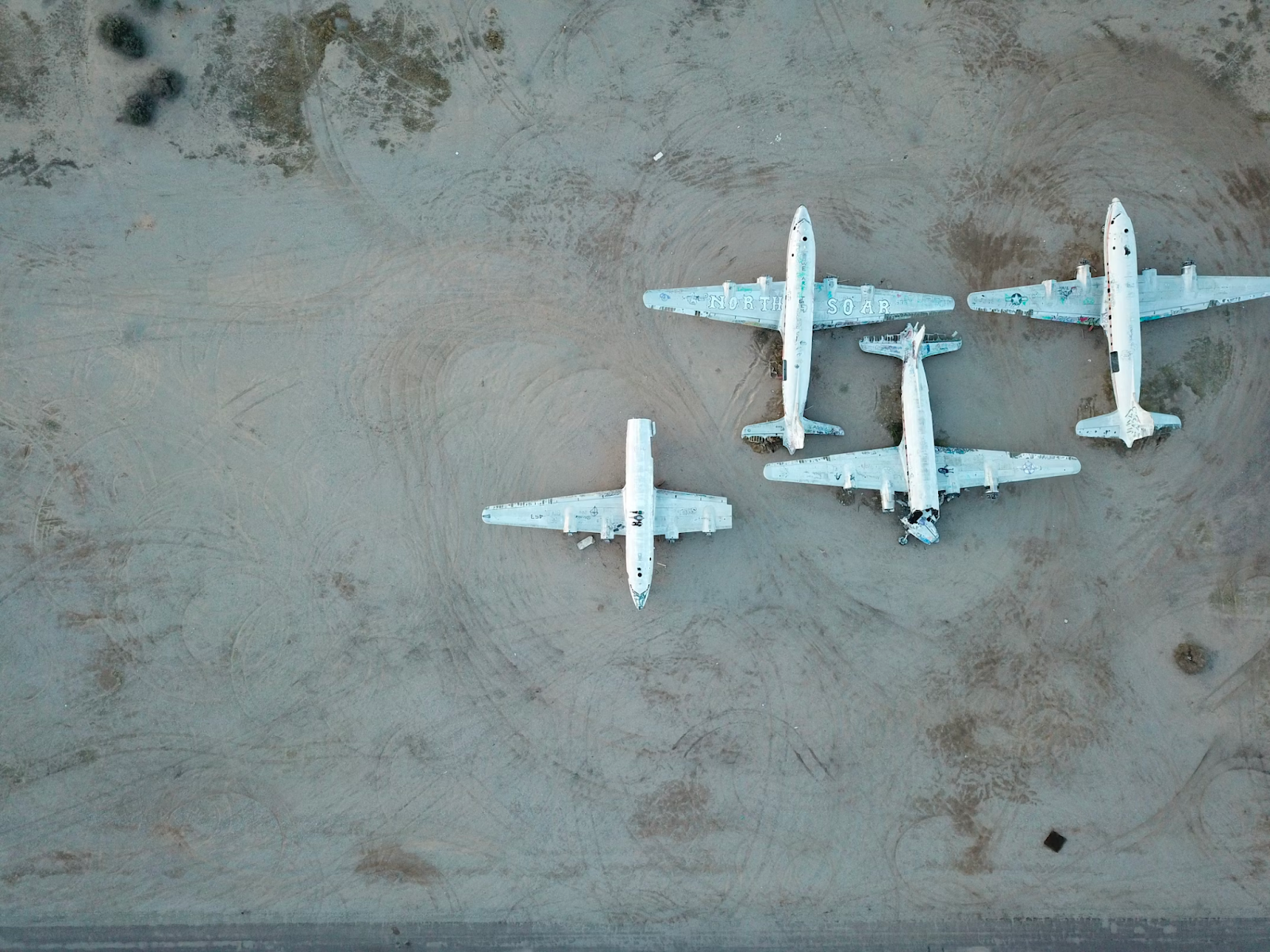
Wind energy
The blades of wind turbines are primarily made from fibreglass-reinforced polymers (FRP) or carbon fibre materials to achieve an optimal balance of strength, flexibility, and lightness. But the wind energy sector is grappling with the disposal of thousands of decommissioned wind turbine blades.
Given the industry's rapid expansion, the amount of composite waste from wind turbines is becoming a significant problem. Based on a report by WindEurope, approximately 14,000 wind turbine blades could be decommissioned by 2023, with an estimated weight range of roughly 40,000 to 60,000 tons. By 2025, blade waste alone will account for 10% of the total projected waste generated from composite materials.7
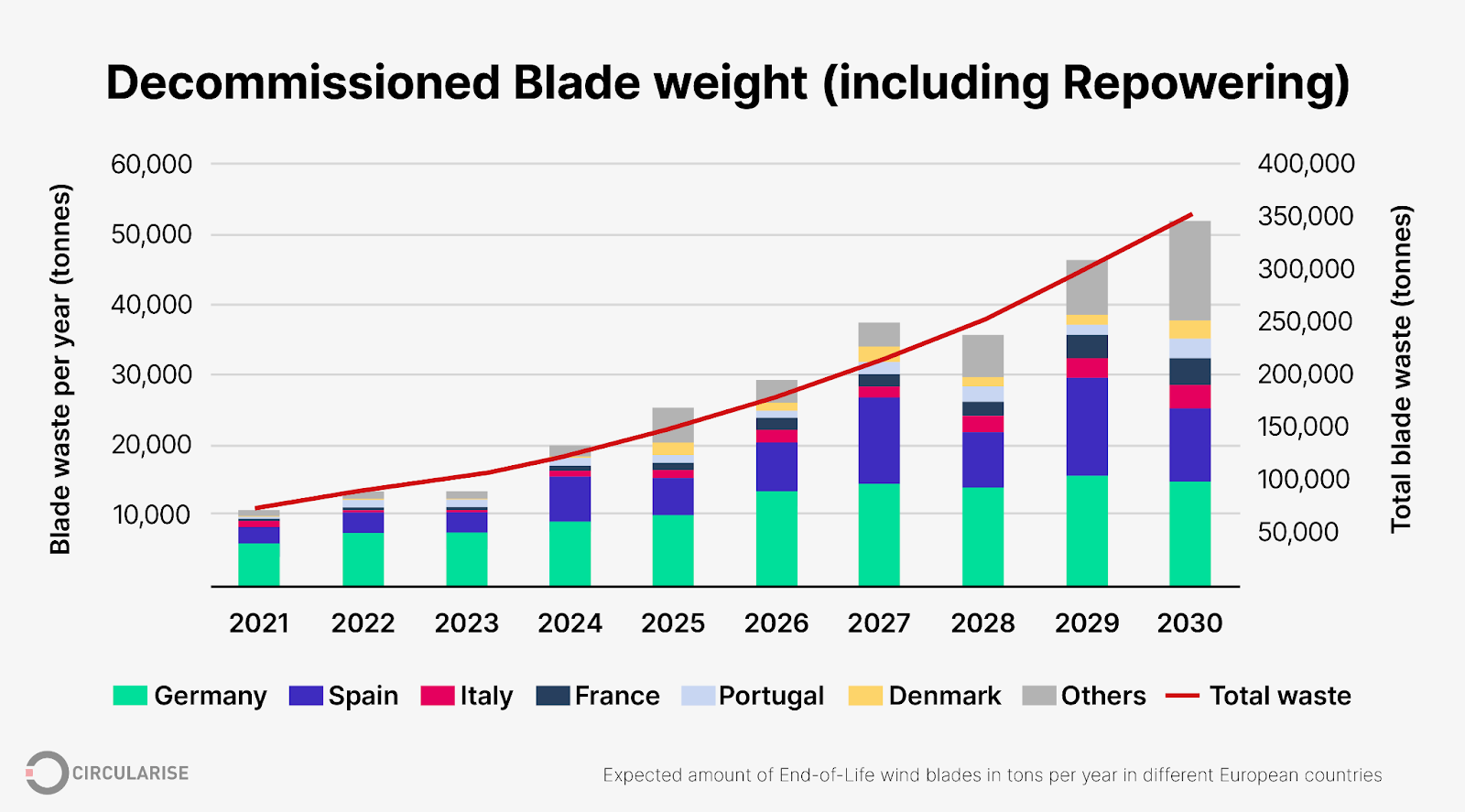
Automotive
The automotive sector employs composites in the production of lightweight and fuel-efficient vehicles. Components like body panels, frames, and interior features are often made from composites, creating waste as vehicles are retired or components are replaced.
While there are no clear estimates on the amount of composite waste generated by the automotive industry, the global automotive composites market is projected to reach 16.3 billion USD by 2030.8 Reports suggest that the EU handles over 6 to 8 million End-of-Life Vehicles (ELV) per year,9 while globally, it is estimated that over 40 million vehicles reach the end of their useful life each year.10
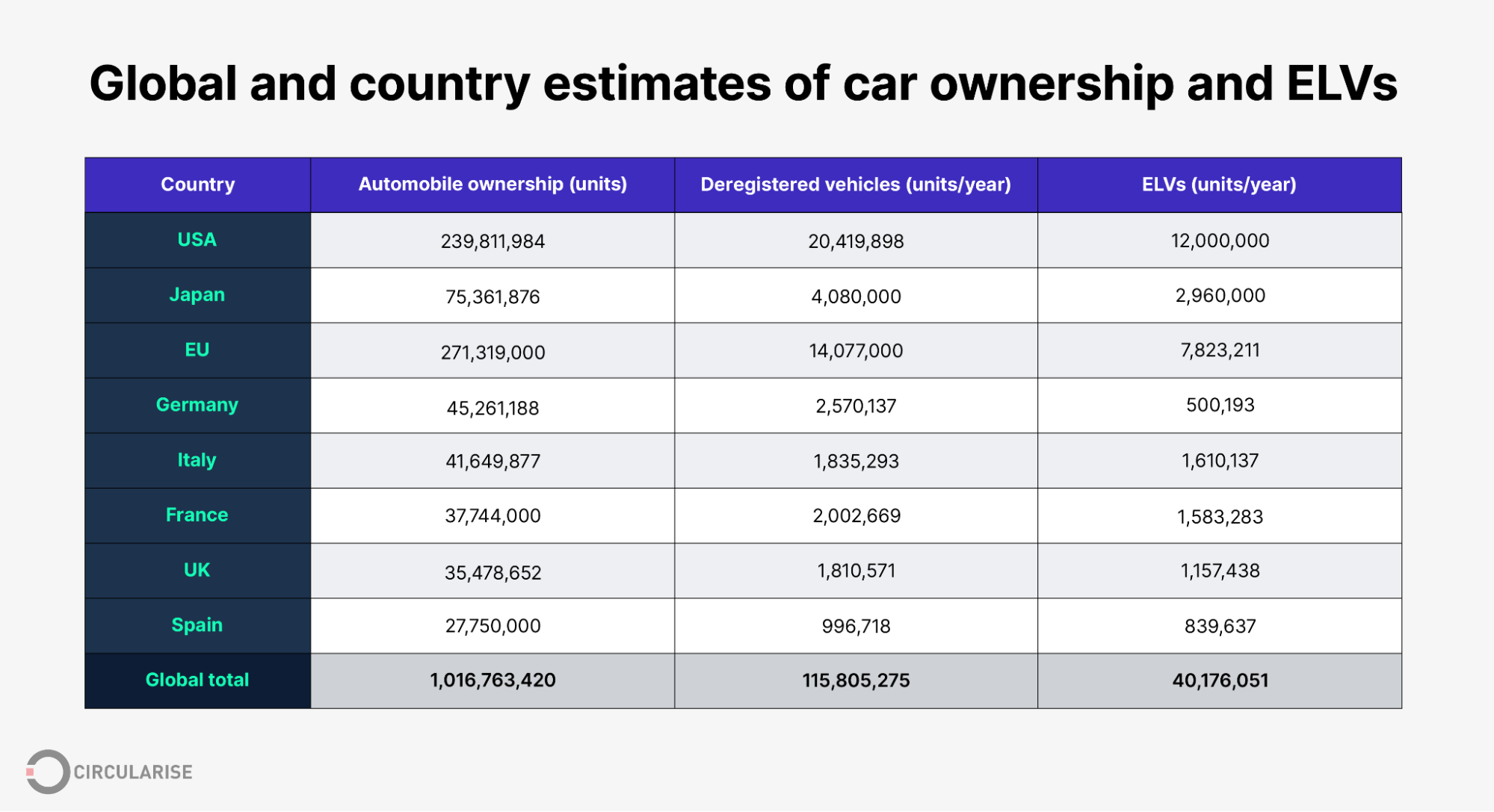
What happens to composite waste?
With these concerning statistics, the effective and sustainable management of composite waste becomes imperative. It is crucial to develop and implement strategies that not only mitigate the environmental impact but also harness the value embedded in these materials. Currently, these are the main methods for disposing of composite materials:11
- Landfilling: The most common way of disposing of composite materials has been to send them to landfills. This is not a sustainable friendly solution, as composite materials can take a very long time to decompose and they can occupy significant landfill space.
- Incineration: Some composites can be incinerated for energy recovery. However, this process can release harmful emissions and leave behind ash that contains hazardous materials, which must then be handled appropriately.
- Recycling: Composite waste recycling encompasses mechanical, thermal, or chemical processes. Each method aims to reclaim valuable materials from composite waste while contending with its own set of challenges and limitations.
- Repurposing and Reuse: Some initiatives focus on finding new uses for EoL composite materials, such as using decommissioned wind turbine blades to create structures like bridges or playground equipment.
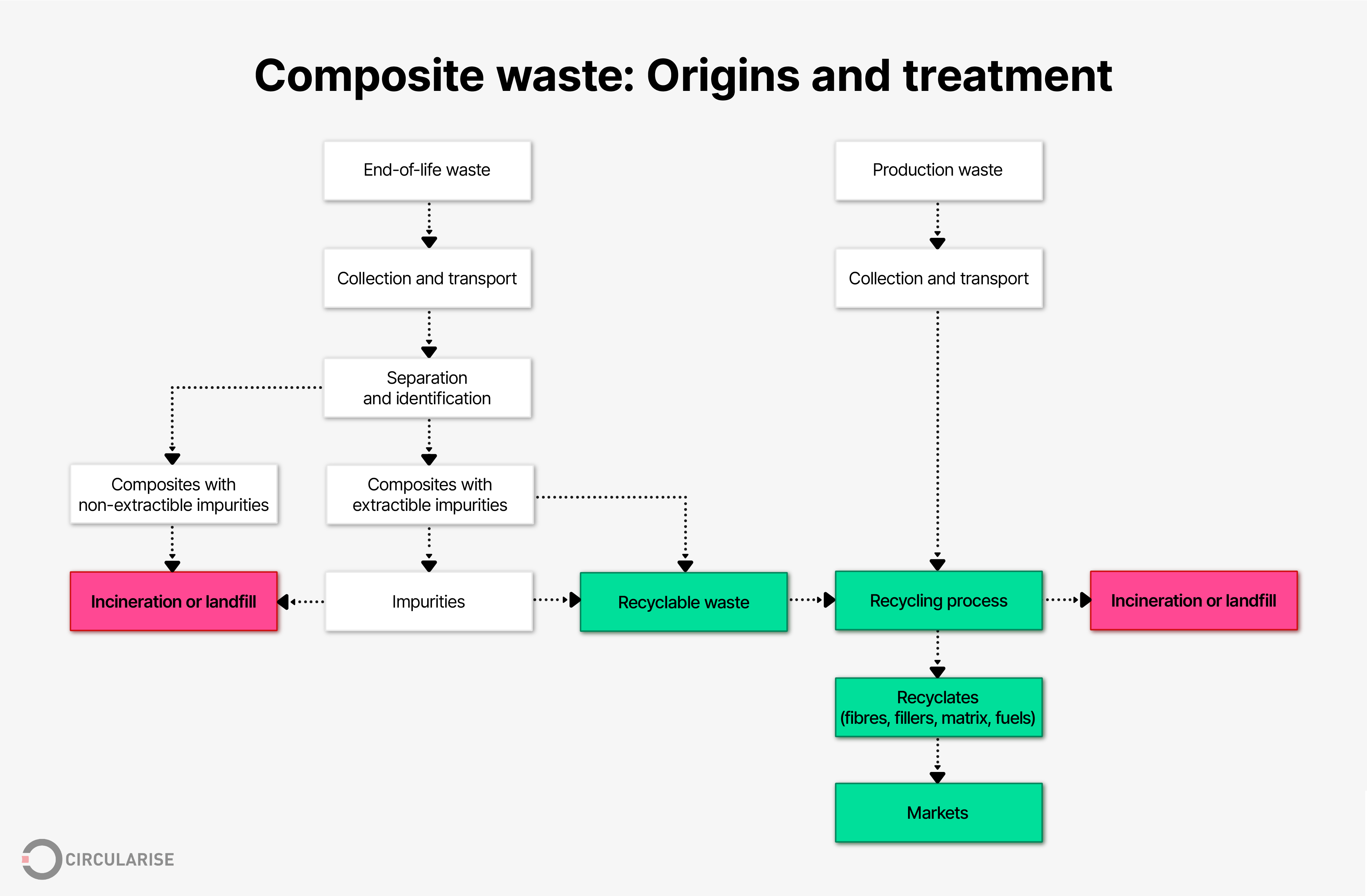
Regulations that impact composite waste
European Commission initiatives underscore the critical need to meet sustainability goals by enacting measures to reduce the volume of products ending up in landfills and encourage companies to develop effective waste management strategies, especially for EoL products.
Non-compliance with these regulations can result in the inability to sell products in the EU, potential fines, and the need for costly redesigns or recalls.
Additionally, as global awareness of environmental issues grows, similar regulations are being adopted in other countries, expanding the impact of this type of legislation beyond the EU. Therefore, manufacturers and companies must carefully monitor and manage the use of hazardous substances in their products to ensure compliance with similar regulations worldwide.
National legislation for composite waste
Many countries already have national waste management legislation that extends to the handling and disposal of composite materials, electronic waste, and End-of-Life Vehicles (ELVs) to ensure that they are managed properly to protect human health and the environment. Recognising the potential environmental hazards and the value of the materials within these wastes, these countries have taken further legislative steps to specifically address these issues:
- Germany enforced a ban on landfilling waste with over 5% organic content in 2009, effectively prohibiting the disposal of wind turbine blades.12
- The Netherlands bans landfilling of composite waste "in principle," but exceptions exist if recycling costs exceed EUR 200 per tonne.13
- France mandates specific recycling rates for end-of-life wind turbines, requiring a minimum of 35% rotor mass reuse or recycling from July 2022, increasing to 45% for permits after January 2023, and 55% after January 2025.1313
- China enacted the “End-of-Life Vehicle Recycling Regulations” in 2001, and amended the “Solid Waste Environmental Pollution Prevention and Control Law” in 2020 to include stricter rules on the production, storage, transport, and disposal of solid waste.14
- Japan's 2005 “Law for the Recycling of End-Of-Life Vehicles” was supplemented with “The Act for Resource Recycling of Electrical and Electronic Equipment and Vehicles” in 2008 to also cover a wide range of electronic products.15
- Korea enforced the “Act for Resource Recycling of Electrical and Electronic Equipment and Vehicles” in 2008 to tackle ELVs and electrical and electronic components.15
Waste Framework Directive (WFD)
The Waste Framework Directive (WFD) establishes the legislative framework for the handling of waste in the EU and could exert a profound influence on the handling of composite waste within the EU.16 While the WFD does not specifically mention aircraft, cars, or wind turbines, it applies to waste generated from these products when they reach their end-of-life stage; specifically:
- End-of-Life Vehicles (ELV) Directive: This is a specific directive within the legislative framework that deals with end-of-life vehicles. It sets out measures to prevent and reduce waste from vehicles and promote their reuse, recycling, and other forms of recovery.
- Waste Electrical and Electronic Equipment (WEEE) Directive: For wind turbines, components such as the generator could fall under the WEEE Directive, which covers the treatment, recovery, and recycling of electric and electronic equipment. This directive could also potentially apply to a wide range of electronic and electrical components found in aircraft and cars.17
The management of waste from these products must comply with the principles of the WFD, which prioritises prevention, reuse, recycling, and recovery over disposal. The directive also requires that waste be managed without endangering human health and without harming the environment.
By mandating member states to create waste management plans that include strategies for composites, the WFD promotes the development of new recycling technologies and marketplaces for secondary raw materials. Extended Producer Responsibility (EPR) schemes, increasingly prevalent in the management of plastics and textiles, could significantly improve the handling of composite waste if similarly applied. This compels manufacturers to consider the entire lifecycle of their products, thus potentially leading to improved design for disassembly and recycling. The directive's impact is steering the EU towards a circular economy, where the environmental footprint of composite waste is significantly reduced.
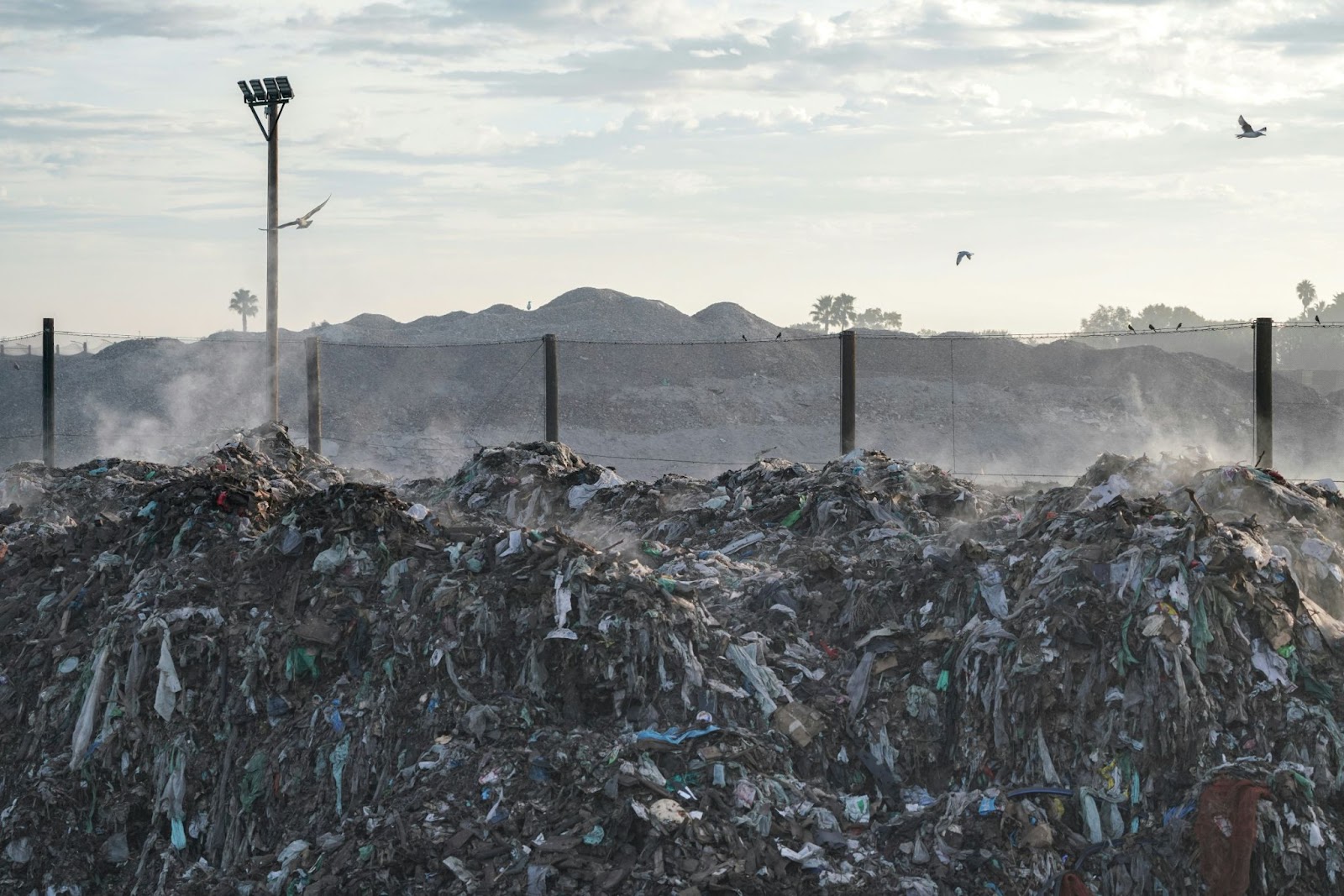
Ecodesign Directive
The Ecodesign Directive (formally known as Directive 2009/125/EC) is a pivotal piece of EU legislation aimed at improving the environmental performance of products throughout their life cycle by establishing requirements for the design of energy-related products. While it primarily targets energy efficiency, the directive also has implications for the broader environmental impact of products, including the use of composite materials. This framework provides overarching guidelines from which more specific product or industry regulations draw their principles, although it does not directly address the issue of composite waste.18
By setting design standards that products must meet before they can be sold in the EU, the directive encourages manufacturers to reduce waste and increase recyclability from the very beginning of the product development process. For industries utilising composite materials, this means a push towards designs that facilitate easier recycling or reuse of components, as well as the potential reduction of hazardous substances in composites, aligning with the EU's goals of resource efficiency and a circular economy.
Eurocodes
This is a series of standards for structural design in the construction and building sector, developed to standardise design practices between EU member states and to increase the performance and safety of buildings against natural and man-made threats.19 The 2nd generation of Eurocodes is being developed since 2010 and it is expected to be published by 2026. Although this is not in effect yet, a preliminary version of the standard for FRP structures has been published and entitled “Prospect for New Guidance in the Design of FRP Structures” which provides guidelines for the upcoming harmonised standard.20
The evolution of these standards can be seen for example for wind turbine blades where they focus now on improving aspects that include component reliability and reduction of maintenance costs, design and certification, as well as EoL management, such as:
- DNVGL-ST-0262:2016 – Lifetime extension of wind turbines21
- DNVGL-SE-0263:2016 – Certification of lifetime extension of wind turbines applies to onshore and offshore wind turbine22
- DIN SPEC 4866:2020 – framework conditions for the sustainable and efficient dismantling, disassembly, recycling and recovery of onshore wind turbines in repowering and decommissioning projects23
- WindEurope – Decommissioning of Onshore Wind Turbines (2020), which proposes amendments to IEC 61400-28 CD Technical Specification Wind energy generation systems – through life management and life extension of wind power assets.24
RoHS Directive
The RoHS (Restriction of Hazardous Substances) Directive is a piece of legislation enacted by the EU that aims to limit the use of specific hazardous materials found in electrical and electronic products. The substances restricted under RoHS include lead, mercury, cadmium, hexavalent chromium, polybrominated biphenyls (PBB), polybrominated diphenyl ethers (PBDE), and four different phthalates (DEHP, BBP, BBP, and DIBP).25
For composite materials, particularly when composites are incorporated into electronic components, RoHS compliance means ensuring that these substances are not used above certain levels in the production process. As a result, the directive influences the composition of composite materials used in electronics across industries.
REACH Regulation
The REACH (Registration, Evaluation, Authorisation, and Restriction of Chemicals) Regulation is a comprehensive framework established by the EU to manage the production, import, and use of chemical substances, and to provide a high level of protection for human health and the environment from their risks.26
Enforced by the European Chemicals Agency (ECHA), REACH requires all companies operating within the EU to identify and manage risks linked to the substances they manufacture and market. Since the precise formulations of composites are not always transparently disclosed, companies rely on their supply chain partners to stay updated with compliance and communicate any potential changes.
For industries dealing with composite materials, this means that any chemicals used in the production of composites must be registered with ECHA. Additionally, producers must assess and communicate potential risks, and may be required to implement risk management measures. This regulation not only affects the choice of raw materials for composites but also has implications for their entire lifecycle, including use, recycling, and disposal, thereby promoting safer use of chemicals and fostering innovation in the development of safer alternatives.
Current initiatives to tackle composite waste
Here are some promising and innovative initiatives in various sectors to find new life for EoL composite waste. Driving these are the R-strategies for circular economy, designed to optimise resource efficiency, minimise waste, and promote the recovery and reuse of materials. Although there are signs of progress, the composite recycling industry is still in its infancy and needs further research and continued investment.
A collaborative, multi-sector approach will be required for developing effective methods to reduce the environmental impact of composite waste. Since each sector produces a relatively small portion of the total waste, pooling resources and expertise across industries, along with guidance from regulatory agencies, will be crucial to developing cost-effective and sustainable waste management solutions.
Circular initiatives in the aerospace sector
The aerospace industry has embarked on initiatives to support these sustainability goals, incorporating recycled materials into their products. This includes innovative practices such as repurposing aircraft components for unconventional uses, transforming them into furnishings, art pieces, or even converting aircraft fuselages into unique hotel structures.27
Efforts to recycle composite materials have been made, with a standout example being the successful collaborative effort between Boeing, VAS, and ELG Carbon Fibre in 2018. This joint venture led to the dismantling of a Boeing 787 and resulted in the recovery of approximately 380,000 pounds of carbon fibre. This recovered material was then sold for reuse to companies in the ground transportation and electronics industries.28
Read about traceability’s role in aviation standards and regulations.
Circular initiatives in the wind energy sector
In a similar vein, the wind energy sector has also pursued various repurposing initiatives.29 For instance, decommissioned wind turbine blades have found a second life as material for building pedestrian bridges in countries like Poland and Ireland.30 Recycled composite materials from these turbines have also been repurposed across the automotive sector, taking on new forms such as short fibre mats, nonwoven mats, carbon fibre yarns, compounded thermoplastic pellets for injection moulding, 3D printing filaments, and discontinuous fibre-reinforced thermoplastic sheets.29
From a sustainability standpoint, the improper management of composite waste can negate the environmental benefits of clean energy, potentially compromising the sector's economic viability and public acceptance. As a result, it is important to also track the lifecycle of the new product made of recycled composite waste.
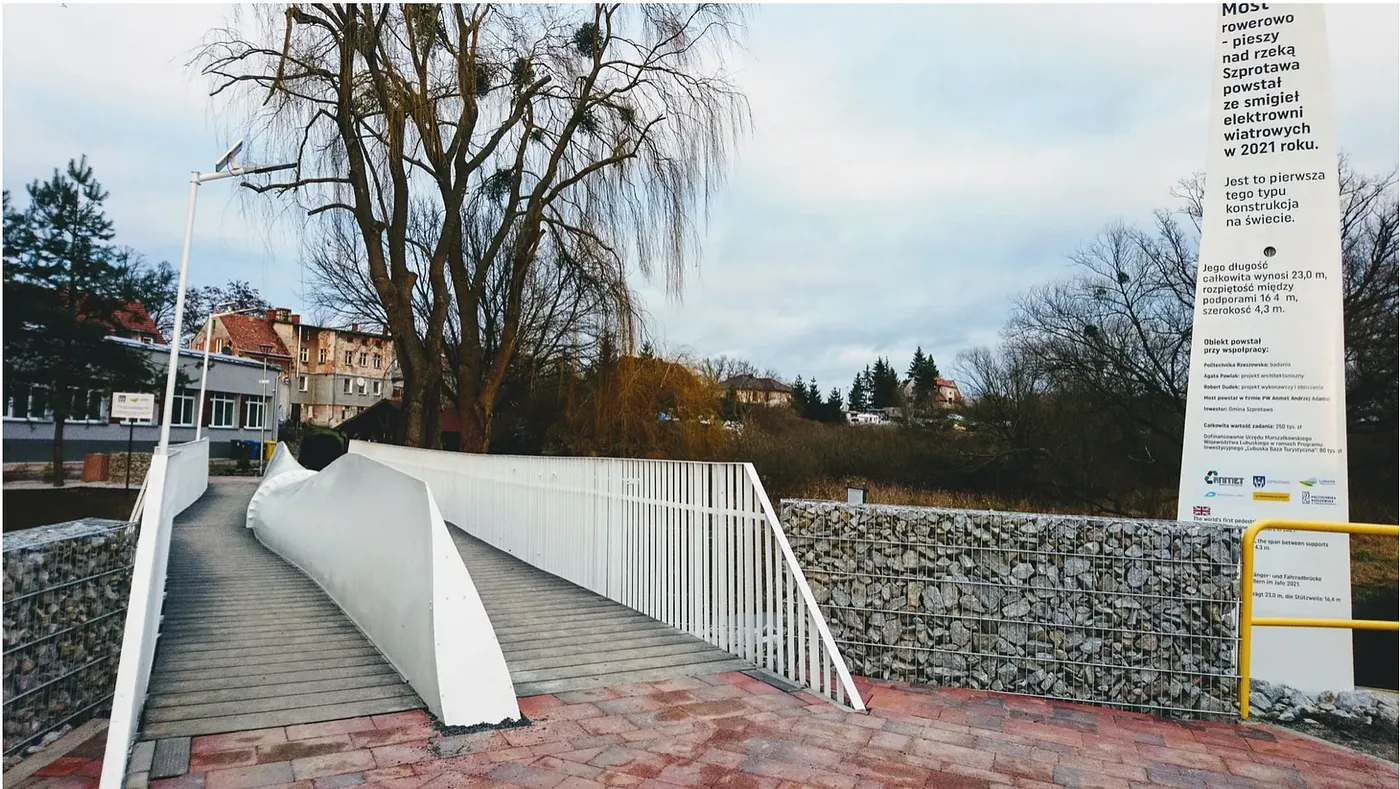
Circular initiatives in the automotive sector
BMW, in collaboration with SGL Group, pioneered a recycling program for the carbon fibre reinforced plastics (CFRP) used in their i-Series vehicles, like the i3 and i8.31 EoL composite components are recycled by being broken down into smaller pieces and repurposed to manufacture new composite parts for non-structural uses due to changes in material properties post-recycling. Beyond automotive applications, BMW also repurposes composite waste for other uses, such as streetlight production and factory construction, showcasing the versatility of recycled composites in reducing waste and resource consumption.32
Find out more about our solutions for the automotive industry.
The EuReComp Project
The EuReComp project is a multi-stakeholder research initiative that aims to develop sustainable recycling and repurposing methods for composite materials, contributing to the EU’s goal of reducing landfill waste.33
Focused on advancing the circular economy for composite materials used in aircraft and wind turbine blades at their end-of-life (EoL), Circularise is working alongside 20 industry experts – including aerospace suppliers, automotive manufacturers, and research institutions in mechanical and industrial engineering – to aid in overcoming the challenges of recycling composites and improving traceability throughout the value chain.
The project's objectives include creating innovative dismantling and sorting mechanisms, improving component reusability, conducting pilot demonstrations, assessing environmental impacts, and collaborating on educational resources to upskill the workforce. Circularise’s blockchain-based software enables secure data sharing for efficient recycling and allocation of EoL components, contributing to the project's goal of creating new products and services that support circular economy strategies and enhance EU industrial competitiveness.
Read more about our role in the EuReComp Project here.
How Circularise can help with the problem of composite waste
Despite the efforts being made across industries to develop more sustainable End-of-Life (EoL) solutions for composite waste, industries grapple with a range of other sustainability challenges, from reducing CO2 emissions to enhancing transparency and navigating changing regulatory landscapes.
The situation is further complicated by stakeholders’ reluctance to disclose sensitive confidential information. Data confidentiality and security are especially crucial for suppliers who handle sensitive information related to intellectual property (IP). Therefore protecting material composition, properties, processes, and upstream chain data is vital for maintaining a competitive edge and preserving unique selling points.
With Circularise’s patented Smart Questioning technology, you can achieve full traceability with privacy across industries. Rather than the full bill of materials, only the essential information needed – such as the presence of certain chemicals (hazardous materials, or that might harm recycling processes, resin system), damages within the EoL parts, repairs or adjustments made throughout the lifetime, mechanical properties and behaviour, among others – is shared for downstream processing. This selective disclosure means that companies can confirm compliance with regulations without revealing proprietary formulations.
Each stakeholder is responsible for selecting what information and how detailed, sharing to whom and updating what is still valid and what has changed in the data regarding their components and processes. This allows for:
- More transparent supply chains, improving EoL decision-making without the need to consult manufacturers for additional data.
- Better resource allocation at EoL, aligning with the appropriate R-strategies based on the condition and lifespan of components.
- Enhanced cross-industry collaboration, as detailed component information at EoL supports the repurposing of materials for structural applications in construction or for recycling into other materials.
Our solution elegantly meets the demands of the aerospace, wind energy, and automotive industries, catering to the requirements of EoL operators by facilitating the collection and treatment of composite waste.
Conclusion
The problem of composite waste is a microcosm of the broader struggle to reconcile industrial progress with global sustainability challenges. As industries continue to benefit from the advantageous properties of composites, they also face the task of managing the resulting waste responsibly. It is a stark reminder that innovation must be coupled with responsibility, and progress with conservation.
The initiatives and regulations currently in place are but nascent steps toward the ultimate goal of a circular economy. The pioneering efforts within the aerospace, wind energy, and automotive sectors to repurpose and recycle composite materials must be replicated on a global scale. Collaborative projects like the EuReComp and technological innovation in traceability and privacy are the building blocks of a future where waste is not an afterthought, but an integral, deliberated element of a product’s lifecycle.
Incorporating robust and scaleable traceability systems into industrial processes will be instrumental in achieving this vision. By streamlining the exchange of critical information while protecting intellectual property, these systems will facilitate the adoption of end-of-life strategies, accelerating the shift towards a circular economy.
Circularise is the leading software platform that provides end-to-end traceability for complex industrial supply chains. We offer two traceability solutions: MassBalancer to automate mass balance bookkeeping and Digital Product Passports for end-to-end batch traceability.