Plastics have revolutionised manufacturing and the durability of countless products. Its usefulness and ubiquity is why 6,300,000 tonnes of plastic waste have been generated since 1950.1 However, 79% of all plastic produced end up in landfills, with the remainder 12% incinerated, and only 9% is recycled.2
This is why innovations are rapidly developing more types of virgin polymers that are made from renewable or recycled raw materials. This circular alternative to the plastics industry would be built on using less fossil resources, more plant-based feedstock, and thus producing less waste.
Research shows that compared with fossil-based plastics, biobased plastics can have a lower carbon footprint and outperform their traditional cousins. Bioplastics can be compatible with existing recycling streams, and some offer biodegradation at the end of life (EOL). But obstacles such as negative agricultural impacts, feedstocks competing with food production, unclear EOL management and higher costs all mean a plastic circular economy, like any transition, must be gradual and calculated for feasibility.
Global consumption and production of plastics remain high, but the progress with is encouraging so far. Global bioplastics production is predicted to increase from around 2.2 million tonnes in 2022 to approximately 6.3 million tonnes in 2027.3 Overall plastic production is >380 million tonnes per year, and increasing at an annual rate of 4%.1
Manufacturers already employing bioplastics in their materials are meeting sustainability goals while also reducing manufacturing and disposal costs. Bioplastics have the potential to reduce carbon dioxide emissions by at least 30% if not more, and their use can lower carbon footprints by 42%. Bioplastics production also consumes 65% less energy compared to traditional petroleum-based plastics.4
This article unpacks the world of bioplastics, explores use cases of the industries benefiting the most from them, and looks toward future implementation, scientific considerations, government policy, and how the mass balance approach and digital product passports can help the plastics industry transition towards a circular economy.
What are bioplastics?
Conventional plastics are derived from natural gas, oil, or plants, while most bioplastics are created through a chemical reaction that converts sugar from plants or other organic materials into the base chemical compounds that go into plastic polymers. When the sourcing of bioplastics replaces fossil resources with abundant, biobased alternatives, biobased plastics can clean up plastics’ reputation with a unique potential of carbon neutrality.5
There are two main types of biobased feedstocks:
- Lignocellulosic and carbohydrate-containing feedstock include sugar cane, corn, wheat, starch potatoes, non-food sources like wood, miscanthus, cardoons and waste streams from agriculture and forestry (straw, bagasse, bark).
- Oleaginous feedstock includes palm oil, soy, sunflower, non-food sources like castor oil and waste streams like tall oil, and used vegetable oils and fats and glycerol originating from biodiesel production.6
Even though these biobased materials are in abundance, it's important to recognise that not all bioplastics are carbon-neutral or biodegradable. Just as there are many fossil-based plastics with a wide range of properties, there is a broad variety of biobased plastics with different properties. biobased contents, and feedstock. As a result, bioplastics can be categorised as either biobased, biodegradable, or in some cases, neither.
It's helpful to unpack these terms. Biobased relates to the ingredients that go into bioplastics mentioned above — the feedstock. Biodegradable has nothing to do with the feedstock. It relates to a property that can be measured on a product level, linked to its chemical structure.
Therefore, a plastic can be 100% biobased – meaning entirely derived from plant materials, yet still not be biodegradable. Conversely, a plastic made entirely from fossil fuels might have the ability to biodegrade.
Types of bioplastics
Biobased refers to the origin of the materials used to make bioplastics — specifically, the raw materials or feedstock. This indicates that the plastic is derived from biological sources, such as plants.
Biodegradable, on the other hand, describes a characteristic of the plastic that is independent of its feedstock. This property is determined by the plastic's chemical structure and indicates whether it can break down naturally in the environment.
Depending on the feedstock and the process to make plastic, biodegradable plastics can still be sourced from petroleum or fossil-based feedstock, and even biobased plastics (BBPs) can be non-biodegradable. The family of bioplastics is therefore divided into three main groups:
- PLA, PHA, and PBS are plastics that are both biobased and biodegradable
- PE, PP, PET, PTT or TPC-ET are biobased or partly so, but are non-biodegradable
- PBAT and PCL are based on fossil resources and are biodegradable
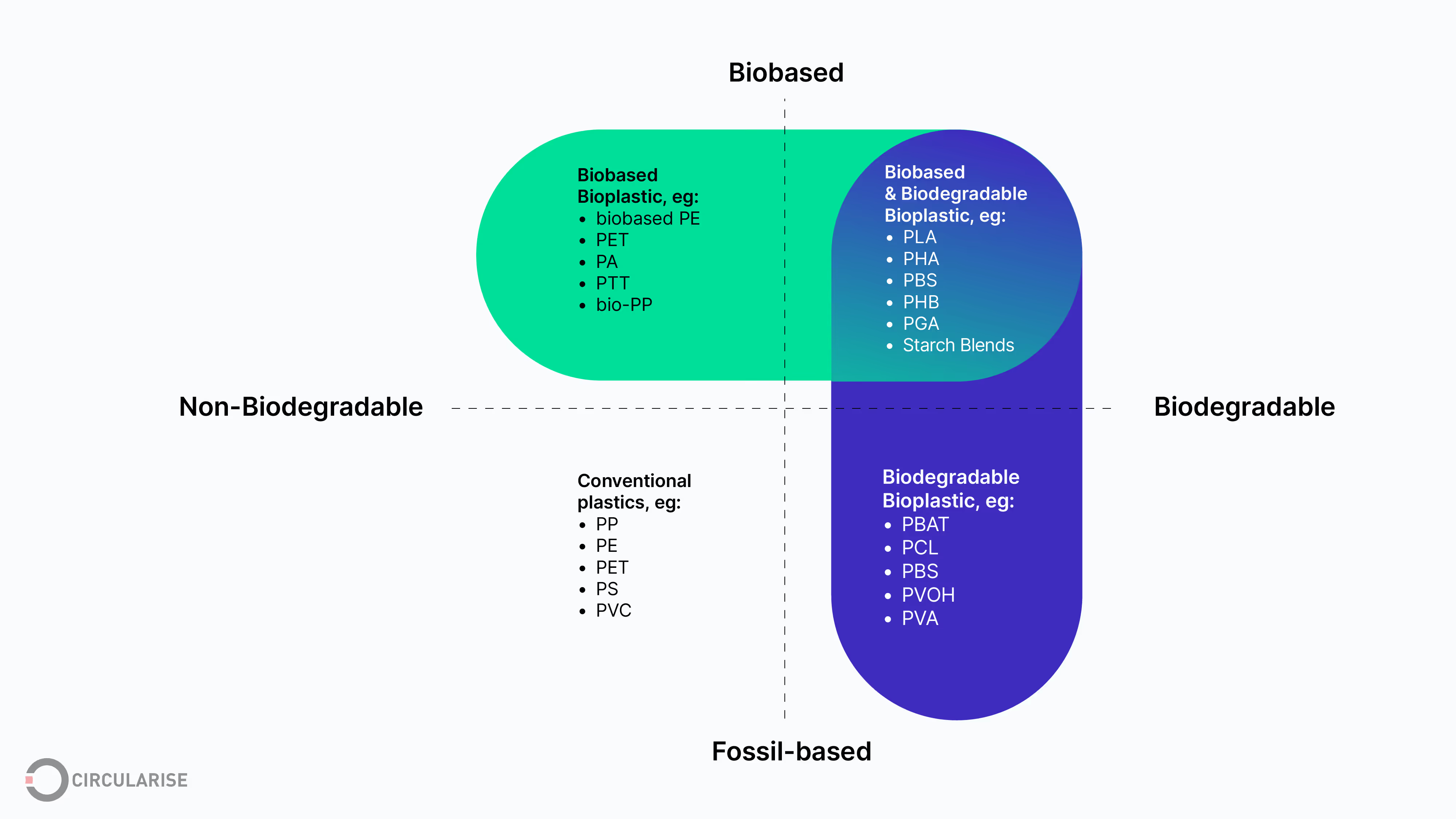
Why are bioplastics important?
Bioplastics are driving the evolution of plastics. The potential of bioplastics will shape the future of the plastics industry. They still represent less than 1% of the more than 390 million tonnes of plastic produced annually, but there is a rising demand for the material, thanks to the emergence of more sophisticated applications and products.
According to a study, simulations reveal that:
- complete replacement of fossil feedstocks with sugarcane would reduce GHG emissions by approximately 25%.
- recycling all existing plastics could have a similar effect.
- switching existing processes to a renewable energy supply would cut plastic-related emissions by 62%.
- halving plastics consumption could lower current levels by 90%.2
Biobased plastics (BBPs) in particular have a unique advantage over conventional plastics. They are made from plant-based resources, which are abundant and renewable. This approach can lead to more efficient use of resources by creating a closed-loop system in which the biomass is first utilised to manufacture materials, and after their use, the same biomass can be converted into energy. By effectively managing the end-of-life of BBPs, we can reduce the risk of microplastic pollution for future generations.7 What’s most exciting about biodegradable plastics is that they can have the ability to be broken down by microorganisms such as bacteria or fungi into water, naturally occurring gases, and biomass.
BBPs also have a lower carbon impact. As global plastic production shifts more from conventional to biobased material origins, this reduces the dependency on limited fossil resources and lowers greenhouse gas emissions — the plastics industry could even become carbon neutral, depending on the feedstock, the product, and the application.8 This aligns with the greenhouse gas emission targets that governments hope will thwart the climate crisis.
The fact that 100% BBPs are produced from plant-based, renewable or recycled raw materials means they can be compatible with existing recycling systems. Emerging chemical and biological methods can also enable the upcycling of plastic waste into higher-quality materials.2 These innovations are considered an important part of future circular economies to help achieve some of the United Nations’ (UN) Sustainable Development Goals.
Market opportunities for bioplastics
Bioplastics are already being used in many products we use in out every day lives. For almost every conventional plastic material and application there is a bioplastic alternative available on the market that has the same properties and potentially offers additional advantages. The portfolio of applications continues to diversify across a wide variety of markets such as textiles to toys, food to electronics.
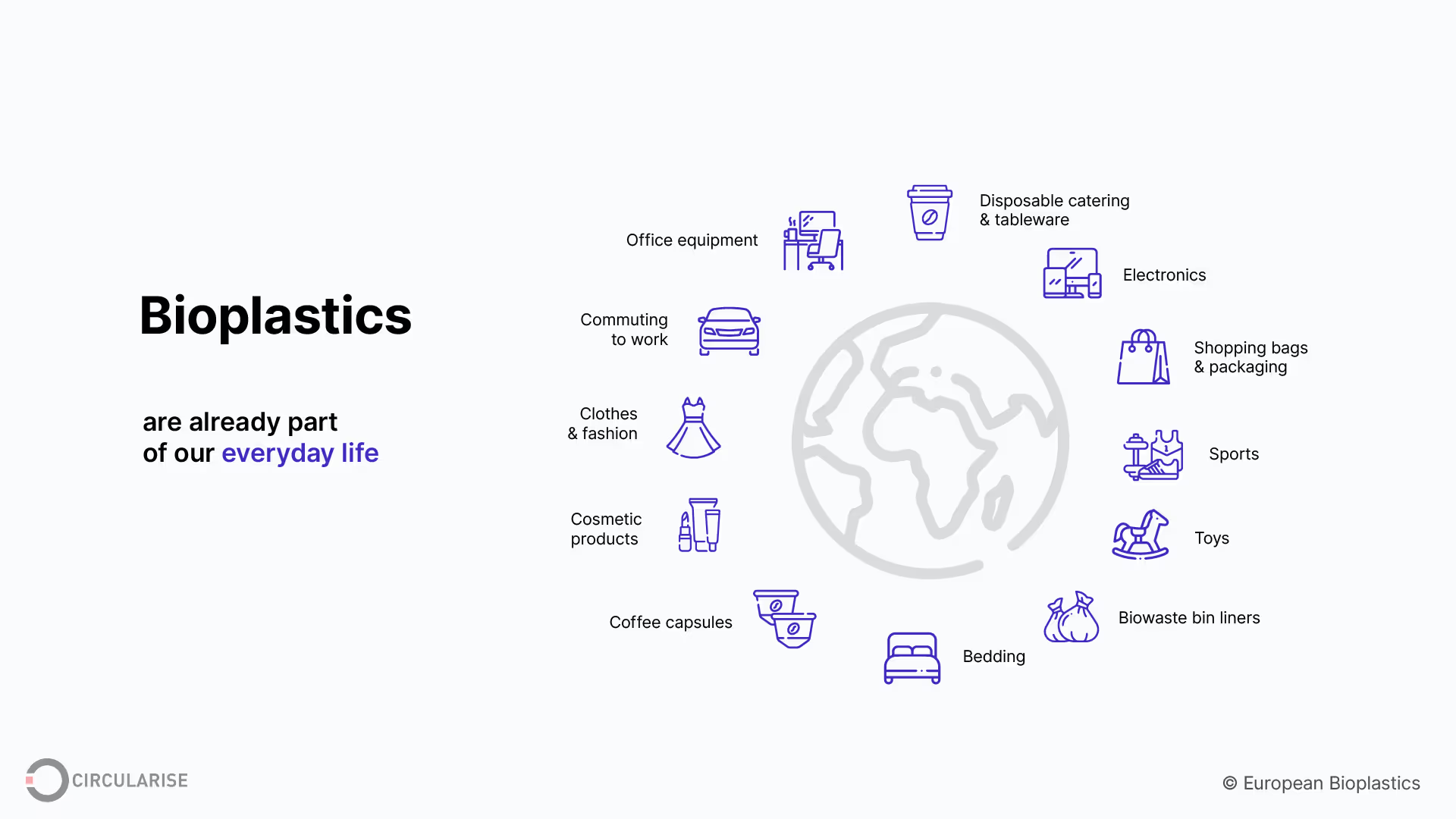
Prospects grow for sectors such as automotive and transport, or building and construction, because functional polymers are growing in their capacity. But packaging is currently the largest market, with 48% of the total bioplastics market in 2022 at almost 1.1 million tonnes.9
Three examples of the sectors that stand to benefit from using bioplastics are the automotive, packaging, and electronics industries:
Automotive industry
The automobile industry is a large source of commercial waste, both during the production phase and at disposal, after the product’s lifecycle. A tremendous amount of plastic waste is generated mainly from the automotive interior, which is not recycled and ends up in landfills, polluting the environment.
An alternative is using polymeric compounds derived from biological sources, which generate a low carbon footprint, limiting environmental pollution and waste management problems. It is also easy to dispose of. Replacing metals with plastics also reduces the vehicle’s overall weight, resulting in a 3% to 7% increase in fuel efficiency.10
Sturdy dashboard components and solid interior and exterior features can be composed of BBPs, while still providing a standard of safety for the transportation sector. The products include seat and airbag covers as well as steering wheels. More specifically, bio-polyamides can be used to make connectors, brake noses, gasoline lines, and flexible tubing. Polylactic acid (a relatively new bioplastic previously used in the biomedical industry) can be used to make mats, carpeting, upholstery, and a variety of under-the-hood components. Bio-based polypropylene can be used to produce bumpers, spoilers, dashboards, air conditioning, battery covers, and air ducts.10
Packaging
The dark reality is packaging represents the greatest source of waste globally. 146 million tonnes was produced in 2015, and 96.6% or 141 million tonnes of that went unrecycled. Packaging tends to have the shortest working life out of all industrial plastic sectors, and the life of single-use plastics can be as short as a few minutes.2
There is a high demand for packaging made from bioplastics for wrapping organic food and premium and branded products. In 2022, global production capacities of bioplastics amounted to about 2.22 million tonnes, with 48% or 1.07 million tonnes of the volume destined for the packaging market – the largest market segment within the bioplastics industry.
The challenge is that a complete switch of global packaging plastics to bioplastics has been estimated to require 54% of the current corn production and 60% more than Europe’s annual freshwater withdrawal. A realistic way to transition would require reduced consumption, improved recycling, along with employing seaweed and other widely available biowaste (although they would require pretreatment processes) to sustainably keep up with production.12
Consumer electronics
A large proportion of consumer electrical appliances are made of plastics, such as casings, circuit boards, and other components of data storage devices. This ensures the appliances are light and mobile, yet tough and durable.
An increasing range of bioplastic products that are being introduced into the sector include touchscreen computer casings, loudspeakers, keyboard elements, mobile casings, vacuum cleaners, or a mouse for a laptop.11 In some instances, it may even offer better heat resistance compared to other traditional plastics.
How increased traceability supports the bioplastics industry
The integration of bioplastics into the mainstream industry, however, is highly dependent on several factors that will take time, effort, and money to achieve. The chemical structure, the manufacturing process and the most likely end-of-life scenario all have to be evaluated across the life cycle, along with metrics such as climate impact, ecotoxicity, and recyclability. Using tools such as a life cycle assessment (LCA) can shed light on the environmental benefits, and increased traceability within the bioplastics supply chain will play a critical role in ensuring the sustainability and ethical sourcing of raw materials.
Read more about the role of taxes, material innovation, and digital traceability on sustainable plastics.
Verification of origins
Transparency along the supply chain allows both manufacturers and consumers to verify the origins of biobased materials, confirming that they are procured responsibly. This level of oversight is key to maintaining the industry's green credentials and building trust with consumers who are increasingly conscious of the environmental footprint of their purchases. Traceability systems help confirm that bioplastics are not only derived from renewable sources but also meet ethical standards, which is essential in an era where corporate responsibility is under tight scrutiny.
Quality assurance and regulatory compliance
In addition to reinforcing sustainable practices, traceability is integral to quality assurance and regulatory compliance. It enables manufacturers to monitor and control the flow of materials throughout the production process, ensuring that the final bioplastic products adhere to stringent standards and specifications. This is particularly important as many countries impose regulations on biobased materials, which may include criteria for biodegradability, compostability, or the inclusion of renewable content.
Supply chain traceability ensures that bioplastic products align with these regulations, facilitating market access and avoiding potential legal pitfalls. Consumer confidence grows when companies can provide guarantees that the products they use are as environmentally friendly as they claim to be.
Read more about complying with global plastic regulations.
End-of-life (EOL) management
The impact of traceability also extends to the end-of-life management of bioplastic products, aiding in the reduction of waste and contamination in recycling streams. By clearly identifying which materials are recyclable, biodegradable, or compostable, traceability supports the correct separation and disposal of bioplastics. This, in turn, optimises waste management processes and minimises the environmental impact of discarded materials. The data collected through traceability initiatives can also spur innovation, leading to improvements in bioplastic materials and production technologies.
As a result, the bioplastics industry is not only able to enhance its products but also to drive growth by delivering on the promise of a sustainable alternative to traditional plastics, thus playing a significant role in the transition to a more sustainable future.
The future of bioplastics
Bioplastics can replace nearly every type of conventional plastic and are diversifying into various markets. But while the growth of bioplastics is promising, their sustainable integration requires addressing resource use, improving supply chain traceability, increasing recycling, and reducing overall consumption. As we look ahead, the bioplastics industry stands on the cusp of a powerful evolution, propelled by a collective aspiration for environmental stewardship and advanced by scientific ingenuity. Innovations in feedstock sourcing and breakthroughs in bioplastic functionalities are set to broaden their applications across industries.
Governments are poised to play a crucial role, with policies that could incentivise the growth of bioplastics and guide responsible production and consumption. The journey towards cost parity with traditional plastics is a critical milestone on the horizon, one that could redefine the competitive landscape.
A major factor for bioplastic adoption to disrupt the plastics industry is the drop-in materials, so-called because these biobased feedstocks act as building blocks that can be a direct substitute for incumbent feedstocks. By substituting with drop-ins, manufacturers can easily facilitate the transition from fossil to biobased. The same processes can be used, rather than establishing entirely new plants, and end-product properties are unchanged.13
However, this also introduces complexities in tracking and attributing the origins of materials throughout the production process. The principle of mass balance is therefore crucial in ensuring that the bio-based content is accurately reflected in the end products. Without third-party certification and meticulous mass balance accounting, there is a high risk that such practices might be perceived as greenwashing.
Digital product passports (DPPs) will play a vital role in scaling bioplastics responsibly, providing the transparency needed to build trust across the value chain. For manufacturers, they ensure that sustainability claims about biobased content are backed by reliable data. For downstream partners, regulators, and consumers, they make it easier to trace and validate the environmental footprint of bioplastic products. In this way, DPPs bridge the gap between innovation and accountability, ensuring that the shift to bioplastics is not only technologically feasible but also credibly sustainable. For a practical overview of how to build one, read our step-by-step guide to creating a digital product passport.
Circularise’s solutions can help companies looking to transition towards utilising more bioplastics for sustainability in several ways. MassBalancer is our mass balance bookkeeping software that can help manage ISCC PLUS certifications for bioplastics. Our digital product passport helps you collect and manage reliable data about your material, product, and supply chain metrics that substantiate your sustainability claims. Read our case study on how Circularise helped DOMO enable scalable mass balance across multiple sites.
As the bioplastics industry matures, it must address the complexities of sustainability and consumer education to ensure that the potential environmental benefits of bioplastics can be fully realised. Thus, the future of bioplastics is not just about creating alternatives to conventional plastics but about fostering a culture of circularity and responsibility that transcends industries and reshapes our environmental legacy.
Circularise is the leading software platform that provides end-to-end traceability for complex industrial supply chains. We offer two traceability solutions: MassBalancer to automate mass balance bookkeeping and Digital Product Passports for end-to-end batch traceability.
Find out how Circularise can help your company move towards sustainability and circularity with our cutting-edge solutions.